DFT
Fabbrica Digitale.
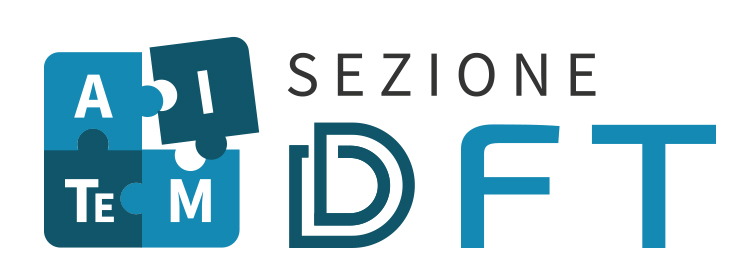
L’adozione industriale di tecnologie digitali ha reso necessarie competenze trasversali per raccogliere, strutturare, analizzare ed impiegare i dati acquisiti. La Sezione DFT (Digital Factory Twin) mira a disseminare le competenze trasversali per lo sviluppo di Digital Twin oltre al know-how necessario per progettare ed operare la complessa infrastruttura digitale richiesta dalle applicazioni industriali. Particolare attenzione è dedicata a interfacce avanzate (Realtà Virtuale e Aumentata) e algoritmi AI.
KEYWORDS
Digital Twin
Fabbrica Virtuale
Intelligenza Artificiale
Formazione/Addestramento
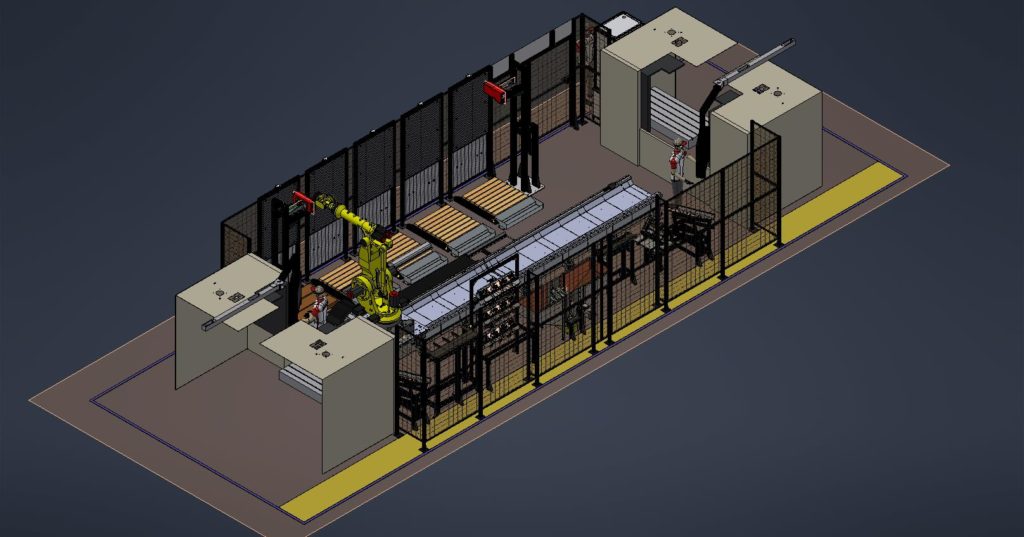
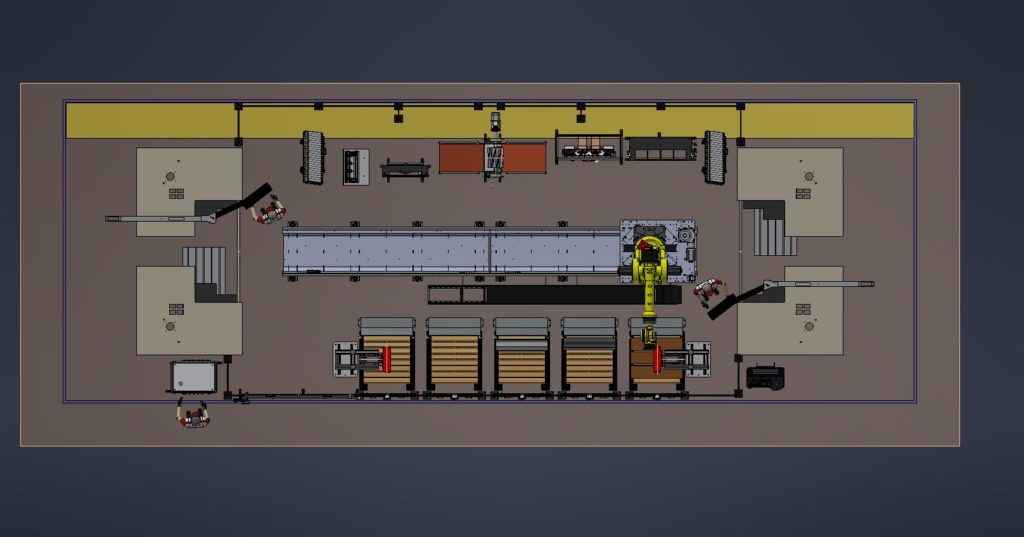
Mission
L’adozione di tecnologie digitali nelle fabbriche ha reso disponibili enormi quantità di dati, ma la raccolta e analisi di questi dati richiedono competenze trasversali (matematica, informatica, ingegneria) oltre ad approcci e strumenti per progettare ed operare la complessa infrastruttura digitale. L’ambito di riferimento di DFT è basato sul concetto di Digital Twin (DT), un gemello digitale di un oggetto fisico a supporto di analisi e decisioni. Nel contesto manifatturiero, un DT può riferirsi a un prodotto, una singola macchina o processo, un sistema di produzione o un’intera fabbrica.
I modelli virtuali che compongono il DT sono utili per la verifica, validazione e valutazione delle prestazioni della controparte fisica lungo le fasi del ciclo di vita. Un efficace DT per il manifatturiero necessita di:
- framework di riferimento a supporto della interoperabilità e comunicazione;
- modelli di dati multi-scala per la rappresentazione di prodotti, processi, sistemi e loro evoluzione;
- sincronizzazione fra fabbrica reale e digitale;
- integrazione di metodologie avanzate che traggono beneficio dal DT.
DFT si pone come obiettivo l’aggregazione di una comunità di ricercatori, fornitori di tecnologie e utilizzatori per lo sviluppo e adozione, in ambito accademico ed industriale, di strumenti di analisi e supporto alla decisione basati su DT di fabbrica. In particolare:
- lo sviluppo di un DT di fabbrica per modellare le caratteristiche di prodotto, processo e sistema per la produzione di componenti meccanici;
- l’integrazione del DT nell’infrastruttura digitale di fabbrica definendo il livello di dettaglio e garantendo la sostenibilità dei flussi informativi e decisionali;
- l’integrazione di strumenti e metodologie a supporto della gestione di un sistema produttivo;
- lo sviluppo di competenze digitali trasversali per gli ingegneri quali nuovi professionisti che dovranno gestire la digitalizzazione delle aziende;
- l’impiego di interfacce avanzate per il training e valutazioni in ambiente virtuale.
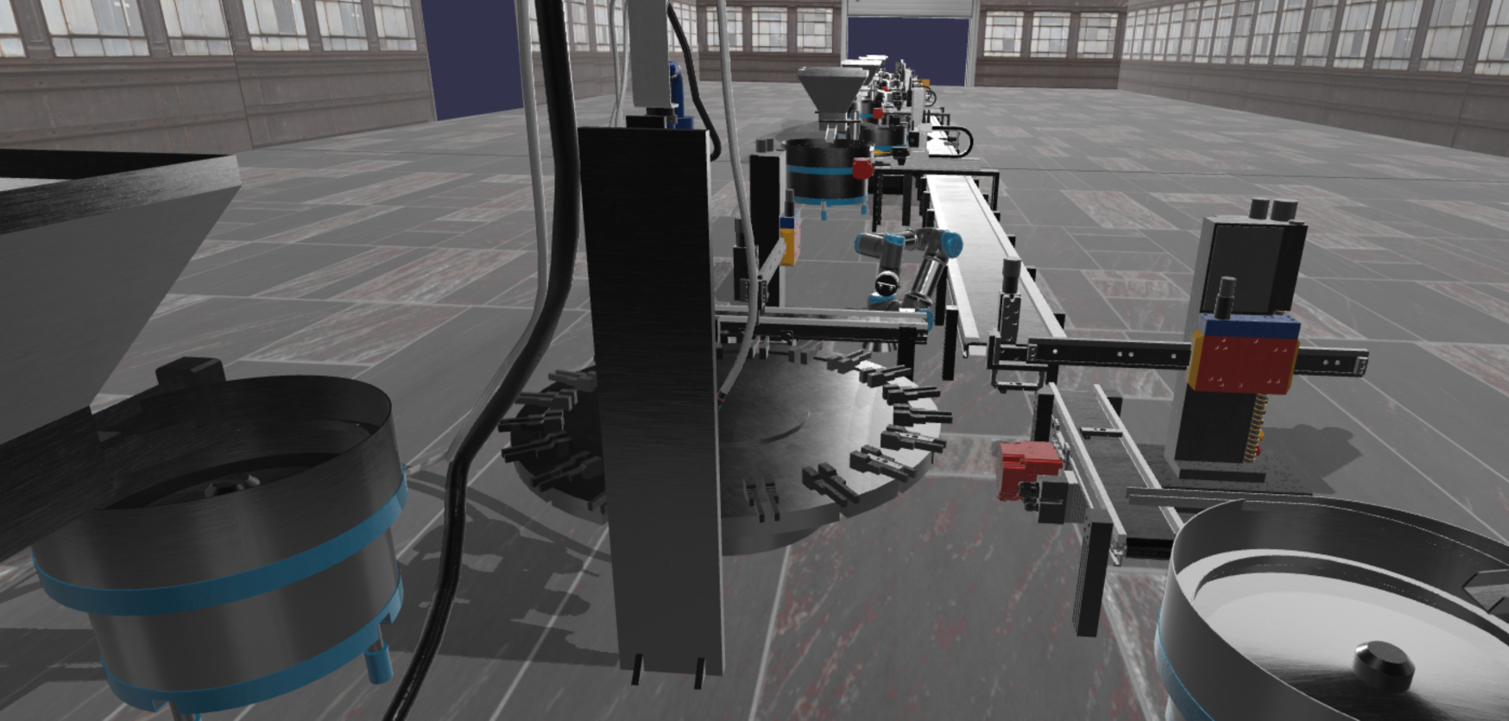
- "I modelli virtuali sono impiegati per la verifica, validazione e valutazione della controparte fisica"
- "Ricercatori, fornitori di tecnologie ed utilizzatori collaborano per adottare strumenti basati su DT di fabbrica"
Coordinatori e componenti fondatori
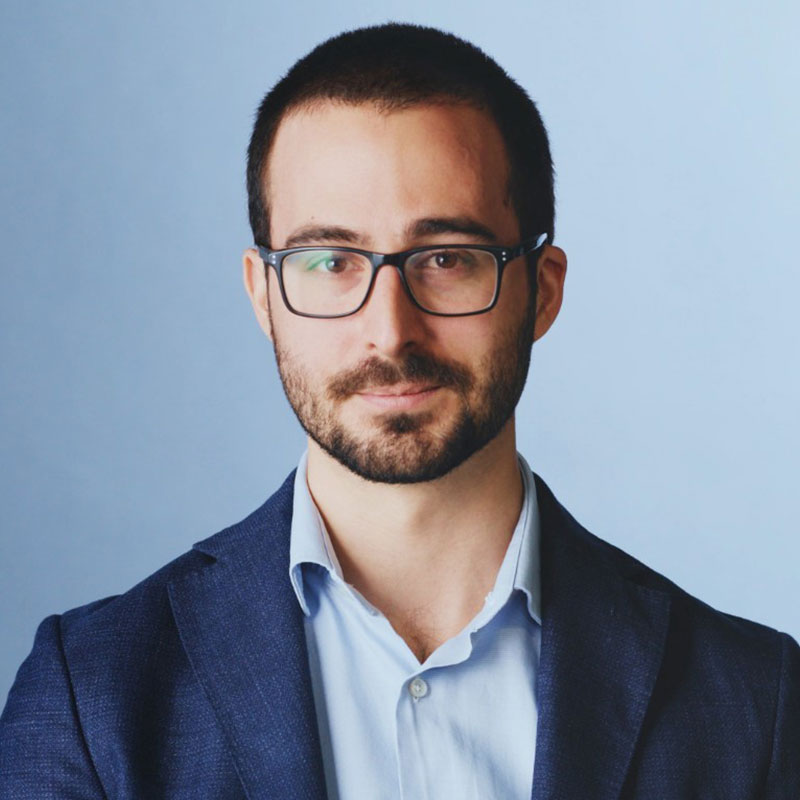
Sortino Francesco
Coordinatore industriale
CELADA SpA
Terkaj Walter, STIIMA-CNR
Sortino Francesco, CELADA SpA
Annoni Massimiliano, Politecnico di Milano, Dipartimento di Meccanica
Sortino Marco, Università di Udine, Dipartimento Politecnico di Ingegneria ed Architettura
Urgo Marcello, Politecnico di Milano, Dipartimento di Meccanica
Pessot Elena, Università di Siena, Dipartimento di Ingegneria dell’Informazione e Scienze Matematiche
Benedetti Fabiano, BeanTech srl
Maisto Saverio, Cluster COMET scrl
Zanelli Riccardo, Cluster COMET scrl
è disponibile il white paper della sezione al link:
https://link.springer.com/chapter/10.1007/978-3-031-41163-2_13